There are numerous ancillary machine tool technologies that shops can use to become more efficient and effective.
• Tool vending systems. A tool vending system can accurately track every nondurable tool for a job while providing daily tool usage reports. This enables tight cost control and ensures that a shop never runs out of the tools it needs. By limiting the number of tools an operator can check out for a given job, the system can also serve as a problem-solving mechanism. If an operator attempts to remove a tool once the limit has been reached, the system can be set up to alert a supervisor who can help the operator determine why an additional tool is needed.
• Tool presetters. Measuring offsets with tools installed in a machine’s spindle can be time-consuming, especially for jobs that require a number of cutters. Conversely, toolholder assemblies for an upcoming job can be measured in seconds using a presetter, without the machine being interrupted. Some presetters generate a label for each tool with the offsets that an operator can quickly enter into the machine’s CNC. Other, more advanced presetters can be networked with the CNC and transfer offsets digitally.
• Machine tool probes. On-machine probes also can speed and simplify setups. A touch-trigger probe installed in a machine’s spindle can find the true location of a workpiece set up on a table and shift the coordinate system to compensate. This eliminates the inherent challenge of accurately positioning parts using dial gages and traditional setup methods. Similarly, a tool-setting probe is an economical solution for on-machine verification of tool geometry and condition. The probe can automatically set length and diameter as well as identify broken tools.
• High-pressure coolant delivery. Compared to flood coolant, a directed stream of high-pressure coolant removes a greater amount of heat, enabling higher material removal rates and faster cycle times. It also helps break up chips and remove them from the cut zone efficiently so the tool spends less time re-cutting chips. Reduced heat and more efficient chip evacuation prolongs tool life and makes replacement more predictable, because the tool wears more predictably.
• Shopfloor CMMs. There are different types of shopfloor CMMs, including the traditional bed-type version as well as articulating arms. Having more advanced shopfloor inspection capability can reduce machine downtime considerably for first-article inspection. That’s because an operator doesn’t have to walk to the quality lab so that a CMM inspector can perform measurement routines beyond what the operator’s conventional gages can support. In some cases, downtime can be extended because the operator has to wait for the lab’s CMM to become available.
The Costs and Benefits of Horizontal Machining
The shift from vertical to horizontal machining was even more expensive than this shop anticipated. It was also more valuable. Most of the shop’s machining centers are HMCs now—here’s why.
Back when Advance CNC Machining of Grove City, Ohio, relied on vertical machining centers, company president Jeremy Hamilton resisted the advice to INVEST in horizontals.
President and owner Jeremy Hamilton has seen the shop grow from serving almost exclusively local customers to serving customers in 24 states and counting
Kyle Dunaway, who is now the company’s VP of manufacturing, was the one advising him to consider HMCs. At a previous job, Mr. Dunaway had worked with HMCs every day. With Advance, he was working with VMCs every day. The difference was apparent to him.
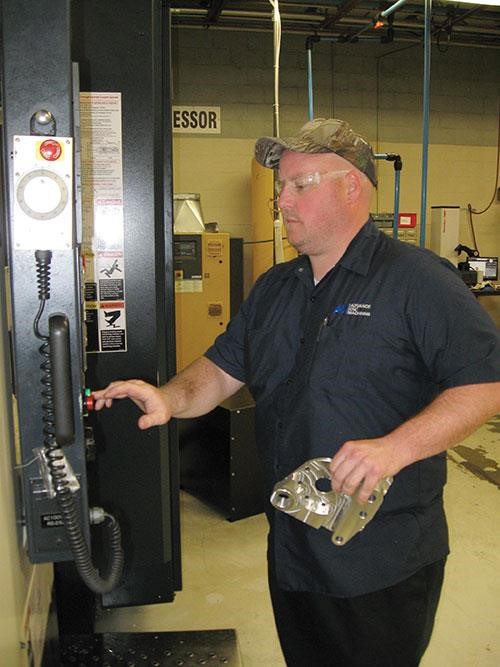
Kyle Dunaway advocated that the shop invest in horizontals.
Ultimately, though, it wasn’t what Mr. Dunaway said that made the case so much as what this employee was able to do—and what most prospective employees were not able to do. The VMC work at Advance often entailed numerous setups, with the part shifted from one vise to another to another, and rotated at each step to present a different face to the spindle. Every step was critical, and every setup had to be precise. Mr. Dunaway, a career machinist, could perform these setups accurately, as could other experienced machinists in the shop. But when Advance needed to expand into a second shift to meet customer demand, the company could not find enough additional hires who had this level of skill.
An HMC seemed like the solution to this problem. Because a horizontal holding a part on a column or tombstone can pivot the work with its B axis to reach various faces in one cycle, fewer setups are needed. Therefore, the shop could buy an HMC to get more capacity, and staff this machine with new employees who had less machining experience. Mr. Hamilton went to a builder he was confident in, Makino, and purchased one of the company’s least expensive HMCs. That was in 2010.
He never looked back. The shop has since purchased HMCs at the rate of about one per year. Today, it has five of these machines. All of the subsequent HMCs have been higher-price models with more features and capabilities than that first one.
Part of what Mr. Hamilton discovered, back when he finally began to use that first horizontal, was that he was wrong in his sense of how expensive an HMC would be. The HMC actually proved to be even more expensive than he had expected, because additional investments were necessary to use the machine effectively.
However, the HMC was also even more productive than he had expected. It was so productive that it more than made up even for the unexpected expense. In fact, starting with the second HMC, the shop began to take advantage of the machine’s speed and precision to implement high-speed machining techniques that leveraged the machine’s capabilities even further. The shop, therefore, went from a different type of machining center to a different type of machining.
Now, even though Advance has raised its hourly shop rate by 50 percent for work it runs on horizontals, it can run work so much faster on these machines that its quoted prices are routinely 25 percent lower than the best it could have achieved when verticals were the only option. The more expensive machine actually enables the shop to win jobs by bidding lower prices.
And Mr. Hamilton says lower price is only the beginning. When work is done on an HMC instead of a VMC, he says his customer benefits in various other ways as well.
Small Batches
Advance’s business is a 50-50 split between maintenance machining—that is, making custom components for plants that are repairing or altering their machinery—and machining production parts. On the production side in particular, Advance is now seeing work it never could have won if not for the HMCs.
One of the two machined parts in the sixth photo at left is an example. On VMCs, the part in the foreground that is machined out of cylindrical STOCK would have required too many setups for the shop to have quoted a competitive price. And even if the shop’s price had somehow been acceptable, its workflow would not have been. To make cost-effective use of all that setup time, the shop would have wanted to machine the entire 2,000-piece order in a single batch, even though few customers want so much inventory at once. Making the part instead in small, incremental batches—what the customer prefers—would be awkward on a vertical, but horizontal machining makes this the natural way to produce.
Indeed, the photo shows this part together with a machined part for a different customer because, on the day the photo was taken, the two parts were being produced in alternating batches on the same HMC. After one machining cycle ran three pieces of the cylindrical part, the machine would swap pallets to run two pieces of the rectangular part while the operator loaded the next set of cylindrical blanks. In this way, shipments for the two different customers were filled simultaneously by one machine through the course of a single shift.
This freedom to keep cutting during job setup or part loading, combined with the horizontal’s benefit of reducing setups by pivoting the part as well as the ability to keep various setups in place and ready to run by using different faces of a column fixture all add up to considerable machine ultilization.
“On a vertical, a highly skilled employee on a good day might be able to keep two machines cutting 75 percent of the time,” Mr. Hamilton says. “With the horizontals, an attentive employee on any day can keep two machines cutting better than 90 percent of the time.”
And then there is high-speed machining, which the shop has been able to cultivate into a particular area of expertise.
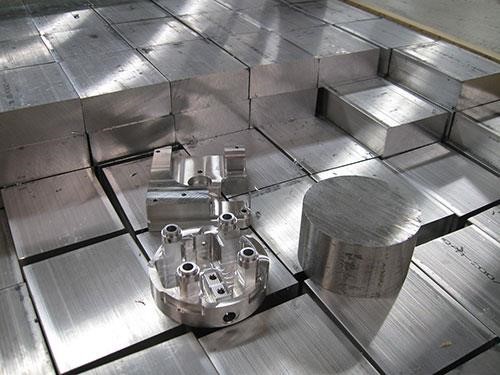
High Feed Rates
On the four Makino HMCs the company purchased after its first, one of the extras the shop opted for was the machine tool maker’s “Super Geometric Intelligence,” a CNC toolpath look-ahead algorithm that permits fast milling by maintaining tight precision at high feed rates. The shop has learned from experimentation how much it can do with faster cutting and how much additional freedom this option gives to its programmers. Often the most efficient way to machine a job is not with deep milling passes, says Mr. Dunaway, but with light milling passes in which the reduced depth of cut is more than overcome by what he previously would have imagined to be an extremely fast feed rate. This same choice can also extend tool life and reduce the variety of tools that have to be used.
The cylindrical part pictured illustrates this as well. Achieving the intricate detail of the part traditionally might have required various tool sizes for rough milling, combined with various other tools for finishing the details. But Advance found it could achieve a much shorter cycle time using a continuously arcing path that keeps one tool at consistent high feed rate and consistent material engagement throughout the milling of this part’s form. Advance used Mastercam’s “Dynamic Milling” feature to generate this tool path, which allows a single small end mill to machine all of the part’s detail except the drilled holes, eliminating the time that would otherwise be lost for tool changes.
Precision at high spindle speeds and feed rates also lets the shop take advantage of newer cutting tool options designed for this kind of machining. Advanced cutting tools were generally counterproductive on the verticals, which lacked the speed and rigidity to use them. Now, tool vendors come to Advance offering samples of new cutters for the shop to try on its HMCs. The ability to capitalize on some of these offerings makes a productive machine more productive still. In one recent case, local Iscar representative Jerry Ward suggested a new high-feed milling cutter that has enabled the shop to realize a significant decrease in cycle time in a deep pocketing operation.
The high-speed machining even makes the HMCs competitive with entirely different types of machines. One machined part resembling a Bundt cake pan was formerly machined entirely through turning, but the shop was burning through turning inserts to machine so much stock out of the round part. The shop switched to the horizontal machining centers instead, milling away the material at light depths and high feed rates. A single end mill now removes an amount of stock that had formerly consumed a dozen or more edges of turning inserts.
Elbow Room
A part Mr. Dunaway cites to illustrate how far the shop has come is one he calls the “elbow,” a component formerly requiring seven operations on three VMCs. The complex part has features at various angles, some of which have to locate accurately with reference to datums on three different faces. He knew the part personally because its setups were so finicky that it was difficult for him to trust anyone else to run it.
Now, plenty of employees run it. Two setups on an HMC accomplish all of the machining. Features referenced to three datums of the part always locate correctly, because those features are now machined in the same cycle as all of the relevant datums. Thanks to the efficiencies of consolidating machining into fewer cycles, plus the gains the shop has realized through high-speed machining, the total machining time for this part has been reduced from 14 hours to 6 hours, and that doesn’t even include saved setup time. On a more expensive machine, the shop has realized a less expensive process.
To be sure, the initial price of the machine was significant. And employing a more capable machine soon led the shop to other investments, such as more capable tooling and workholding, better coolant and better inspection, and even steps the shop had never taken before such as presetting. (See the short companion article below.) However, in the case of each of these investments, what the shop was doing was raising its game, and that eventually brought the shop up into a different league.
“We used to compete with numerous small job shops,” Mr. Hamilton says, but “we rarely have to do that now.” Instead, the shop now bids on work for which the smaller shops don’t have the capability.
Advance also no longer serves just its local MARKET. With the help of a marketing manager and a quality website, the company has taken its more efficient capabilities and gone national. Today, prospects find the shop from far away. Advance has customers in 24 states and counting. The INVESTMENT continues. All of those previous expenses have paid dividends, and this bigger league is where Mr. Hamilton wants his company to keep playing. Thus, he says he is no longer so resistant about spending money where it is needed. For example, he intends soon to address a missing qualification that has shut his shop out of the chance to bid on some recent jobs. The next step, he says, will likely be ISO certification.