Computer Numerical Control (CNC) machine tools are computer controlled pieces of equipment with a number of material forming applications. Each machine follows certain protocols designated by its CNC software.
DrillsCNC machine drillsfollow specific instructions in the manufacturing of a part. A software platform can control the position of the cut, as well as the depth of the hole being drilled. Computer control is used when the work piece requires repeated drilling or tapping cycles. Certain parameters, such as depth, feed rate, retraction and cancellation of the cycle control the drilling sequence.
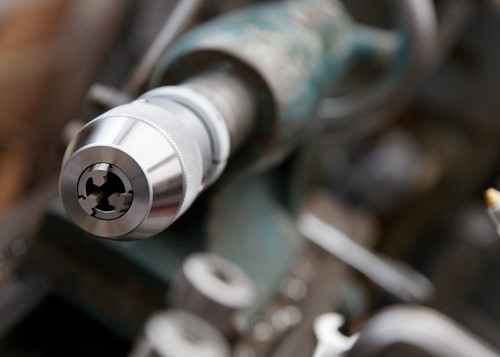
Lathes A lathe is a machine that spins a part in place while a cutting blade removes excess material to prepare it for deformation . Lathes can be used for cutting, sanding, drilling, knurling, or deforming. Cutting fluid may be used to remove the swarf (debris), and to serve as a lubricant or coolant during the cutting process. CNC lathes are often used in the production of camshafts and crankshafts.
Electrical Discharge Machining Machines (EDMs)
Electrical discharge machining is a technique for making minute, complex cuts or contours in hardened materials that would otherwise be difficult to shape. EDM is only effective on electrical conductors, and is used mainly on ferrous alloys. EDM machines fire a series of rapid electrical bursts from an electrode to melt or vaporize material. The remaining debris is flushed away with dielectric fluid.
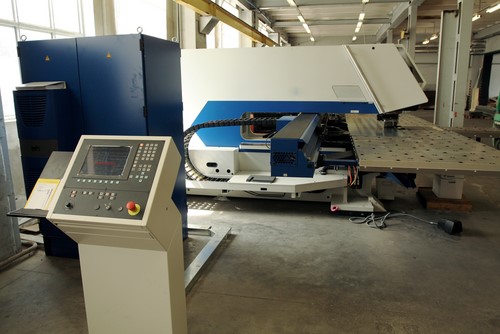
Milling Machines
Milling machines are used to make complex shapes out of metals and other solids. A work piece is fixed to a moveable table that guides the material around a stationary rotating cutter, or, inversely, a moving cutter operates across a stationary table.Some of them also feature a spindle that can be moved along its Z-axis, thus offering a more adjustable cutting method. Milling machines are commonly used for planing, drilling, rebating, routing, and slot cutting. In addition, machines equipped with the Z-axis spindle can be used to create advanced three dimensional objects, such as relief sculptures. Milling machines can also be used for die-sinking and engraving projects.
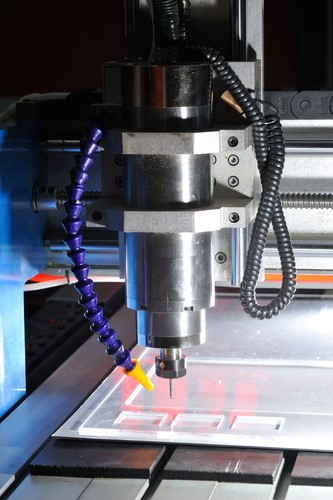
Plasma Cutting Machines
CNC plasma cutters use a plasma torch to cut material under the direction of a software program. A computerized torch head slices a work piece along the axes of a CNC table, often preparing welding seams for the manufacture of multi-part components. Plasma cutting can usually handle thick material, and the process is frequently used in the production of ducts and vents.
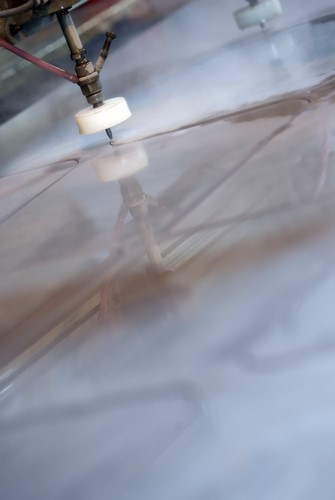
Water Jet Cutter Machines
Water jet cutting simulates erosion by using a stream of high-pressurized water (sometimes in combination with an abrasive , such as grit or aluminum oxide) to cut through material. The process reduces the risk of heat-damaging the work piece, and though it can be applied to a wide range of materials, some substances are impervious to it. As in other CNC systems, the table or the jet mechanism are under computer control.
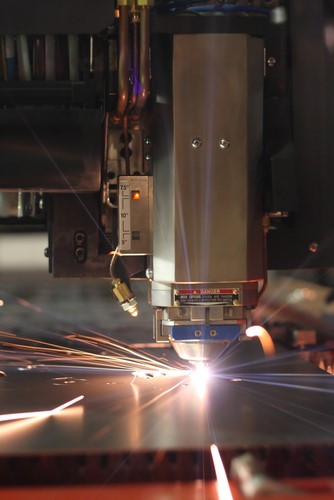
Laser Cutting Machines
Laser cutters use a high-powered laser to shape work pieces. Since the excess material usually melts, vaporizes, or is blown away from the cut, the process can yield clean, high quality finishes. CNC lasers can provide improved accuracy due to the precision of computer controlled cutting.
Oxy-Fuel Cutting Machines
Oxy-fuel cutters use a torch to heat ferrous metals to their kindling point and apply a pressurized stream of pure oxygen to cause a chemical reaction in which slag is channeled away from the cut. These cutters are powered with gases, such as acetylene, and a CNC program guides both the torch and the oxygen release rate.
The Programming and Processes of CNC Machining
Many CNC machines employ a numerical control programming language that uses preparatory codes, or “G-Codes,” to coordinate the tool and initiate its work orders. Three dimensional models generated in computer aided design (CAD) programs are converted into CNC code through computer aided manufacturing (CAM) software before work can begin.
There are roughly four stages in the CNC manufacturing process: roughing, semi-finishing, finishing, and contour milling. Here is a brief outline of each step:
- Roughing begins with the introduction of the raw STOCK, or billet, which is cut into the approximate shape of the final product.
- Semi-Finishing employs raster passes, constant step-over passes, waterline passes, or pencil milling techniques to hone the material closer to its final shape.
- Finishing initiates a faster spindle rotation speed and a decreased material feed rate. This step produces applies a finer finish to the piece.
- Contour Milling is usually used on hardware with five or more axes. During contouring, the work piece is rotated to allow a cutting tool to finish the part with higher dimensional accuracy. Contour milled components can have greatly improved surface finish.
As CNC software and computer hardware becomes more cost-efficient, it may be useful for manufacturers to consider including computer-controlled tools in their shops. The relative precision, uniformity of products, and standardization of methods that CNC tools provide can make them a valuable addition to a range machining projects.
Modes of use OF Lathe machines
When a workpiece is fixed between the headstock and the tail-stock, it is said to be “between centers”. When a workpiece is supported at both ends, it is more stable, and more force may be applied to the workpiece, via tools, at a right angle to the axis of rotation, without fear that the workpiece may break loose.
When a workpiece is fixed only to the spindle at the headstock end, the work is said to be “face work”. When a workpiece is supported in this manner, less force may be applied to the workpiece, via tools, at a right angle to the axis of rotation, lest the workpiece rip free. Thus, most work must be done axially, towards the headstock, or at right angles, but gently.
When a workpiece is mounted with a certain axis of rotation, worked, then remounted with a new axis of rotation, this is referred to as “eccentric turning” or “multi-axis turning”. The result is that various cross sections of the workpiece are rotationally symmetric, but the workpiece as a whole is not rotationally symmetric. This technique is used for camshafts, various types of chair legs.
Choice of machines and control type
Mechanical screw machines have been replaced to some extent by CNC lathes (turning centers) and CNC screw machines. However, they are still commonly in operation, and for high-volume production of turned components it is still often true that nothing is as cost-efficient as a mechanical screw machine.
In the hierarchy of manufacturing machines, the screw machine sits at the top when large product volumes are needed. An engine lathe sits at the bottom, taking the least amount of time to set up but the most amount of skilled labor and time to actually produce a part. A turret lathe has traditionally been one step above an engine lathe, needing greater set-up time but being able to produce a higher volume of product and usually requiring a lower-skilled operator once the set-up process is complete. Screw machines may require an extensive set-up, but once they are running, a single operator can monitor the operation of several machines.
The advent of the CNC lathe (or more properly, CNC turning center) has blurred these distinct levels of production to some extent. The CNC turning center most appropriately fits in the mid-range of production, replacing the turret lathe. However, it is often possible to produce a single component with a CNC turning center more quickly than can be done with an engine lathe. To some extent too, the CNC turning center has stepped into the region traditionally occupied by the (mechanical) screw machine. CNC screw machines do this to an even greater degree, but they are expensive. In some cases they are vital, yet in others a mechanical machine can match or beat overall performance and profitability. It is not unusual for cam-op automatic lathes to beat CNCs on cycle time.[3] CNC offers many benefits, not least CAD/CAM integration, but the CNC itself usually does not give any inherent speed advantage within the context of an automatic lathe cycle in terms of speeds and feeds or tool-changing speed. There are many variables involved in answering the question of which is best for a particular part at a particular company. (Overhead is part of the calculation—not least because most cam-op machines are long since paid for, whereas a late-model CNC machine has hefty monthly payments). Businesses relying on cam-op machines are still competing even in today’s CNC-filled environment; they just need to be vigilant and smart about keeping it that way